Digging Deep: Critical Mineral Supply Chains, Electric Vehicles, and the Role of Technological Innovation
This issue brief considers how innovation may impact supply chains for EV critical minerals and the various policy challenges in scaling up nascent technologies.
1. Introduction
Growing adoption of electric vehicles (EVs) increases the demand for critical minerals used in EV batteries and motors. The stability and reliability of supply chains for these materials are significant concerns because of the geographic concentration of supplies. While supply-side policies such as development of new sources are important, so is innovation in both recovering and processing minerals and in battery and magnet designs that affect mineral demands.
This issue brief considers questions related to innovation that affects supply chains for EV critical minerals and the policy challenges in scaling up nascent technologies for commercial deployment. It is motivated by a March 2024 webinar organized by Resources for the Future with experts from academia, the automotive industry, and the federal government.
2. Technological Innovation as a Response to Supply Chain Concerns
Innovation increases opportunities for improving productivity or helping mitigate other risks. In the context of EV battery minerals, innovation may help accomplish several goals in strengthening supply chains:
- Enhancing and diversifying primary production. The focus here is on innovation that improves access to previously uneconomic resources in diverse locations. This can help reduce the risk of high prices from rising scarcity of critical minerals.
- Improving secondary sources (e.g., recycling) and manufacturing process efficiency to reduce material waste. This can mitigate important environmental risks while also complementing primary supply sources to reduce scarcity risks over the longer term.
- Increasing substitution possibilities. Technological innovation can enable substitution in various ways: material substitution, where one element or material is substituted for another; process substitution, where an innovative process improvement can lead to economizing the use of a particular material while achieving the same product properties; and system substitution, where an entire component or system can be replaced. Substitution can reduce risks from rising scarcity or supply instability for certain critical minerals. It also can reduce environmental and social risks from extracting and processing certain minerals.
Categories 1 and 2 concern the supplies and costs of critical minerals. Category 3 relates to critical mineral demands. An interest in making EV critical mineral supply chains more environmentally sustainable cuts across all three innovation categories. That includes preparing for when EV batteries and rare-earth magnets approach the end of their useful lives, as in category 2; reducing the environmental footprint of primary production, as in category 1; and using battery designs that reduce the overall environmental footprint of battery production, as in category 3.
Each of these goals involves uncertainty. We do not know when primary supplies will dwindle to the point that innovative extraction methods and greater reliance on secondary sources will become economical. We do not know if or when supply or cost uncertainties for particular critical minerals might imply a need for alternative battery or magnet designs. We do not know if or when the environmental footprint of critical mineral extraction, processing, and utilization will pose a threat to environmental sustainability on a larger scale. In addition, the process of technological innovation itself involves uncertain results. Government and private sector managers of innovation processes must weigh the comparative risks and rewards.
3. Examples of Technological Innovation Relevant to EVs
3.1. Enhancing and Diversifying Primary Production
Innovations to increase primary sourcing for battery materials are underway, with support from industry and the US Department of Energy (DOE) under its Critical Minerals and Materials program. The efforts include improved processing to capture more usable minerals from ores and other raw materials and new techniques for recovering minerals, including battery minerals (lithium, cobalt, manganese, nickel) from unconventional sources such as tailings or legacy mines.
Direct lithium extraction(DLE) is a technology that has the potential to rapidly increase the supply of lithium at sites where solar evaporation currently is used to evaporate lithium-containing brines. DLE can provide higher recovery rates and can extract lithium more quickly than solar evaporation. It also can enable lithium extraction from unconventional sources such as geothermal and oilfield brines. It is expected to be more environmentally friendly than other technologies, with lower land and energy requirements at brine sites. Water requirements for DLE vary based on the type of DLE technology, with some types needing less water than conventional brine extraction while others need more. In cases where large quantities of water are needed, innovation around water usage facilitates successful commercialization of DLE.
High-voltage pulse technology, which uses short-pulsed electrical discharges to selectively break mineralized ores while keeping adjacent barren rocks intact, is in the process of being commercialized. High-voltage pulse technology’s deployment could improve energy efficiency in mining and make it possible to send mineralized ores to the processing plant while leaving behind material that contains little or no mineral.
3.2. Improving Secondary Sources (e.g., Recycling) and Manufacturing Process Efficiency to Reduce Material Waste
EC-Leach is an innovative recycling technology developed by researchers funded by the Critical Materials Innovation Hub (CMI), a DOE Energy Innovation Hub. This technology uses fewer chemical inputs and requires lower temperatures than conventional recycling methods to promote the recapture of value streams from end-of-life lithium-ion batteries. Hydro-to-Anode process technology is another innovation in recycling. Developed by Ascend Elements, it enables recapture of 99.9 percent pure graphite from anode materials in end-of-life lithium-ion batteries.
Technological innovation to improve manufacturing process efficiency has come from the development of software packages that are designed to optimize the operation of gigafactories by improving battery cell yields. Among other things, this expedites facility startups. Honeywell has developed one such software known as Battery Manufacturing Excellence Platform. The software allows manufacturers to detect and resolve quality issues before they result in scrapped material; the company claims the process could reduce startup material scrap rates by 60 percent and increase delivery rates.
3.3. Increasing Substitution Possibilities
Increasing substitution possibilities requires innovation in battery (or EV motor) design and may also require innovation in producing and processing minerals used to substitute for existing inputs. All forms of substitution typically take time for reengineering of production lines and may involve some retraining of the workforce.
An example of material substitution, where one element is substituted for another, is the increased substitution of nickel for cobalt in lithium-ion batteries using nickel-cobalt-manganese chemistry in their cathodes, as a response to human-rights concerns associated with the extraction of cobalt in the Democratic Republic of Congo.
An example of material substitution, where one material is substituted for another, is the substitution of rare-earth-free iron nitride permanent magnets for rare-earth-containing neodymium-iron-boron (NdFeB) permanent magnets used in EV motors. Efforts are reportedly underway to develop a process for mass production of these rare-earth-free permanent magnets. Another example is the substitution of a different battery chemistry such as a lithium iron phosphate, solid-state, or sodium-ion battery for the lithium-ion battery in an EV that uses nickel-cobalt-manganese chemistry.
An example of innovative process improvement, which can lead to economizing the use of a particular material while achieving the same product properties, is selective usage of dysprosium in the fabrication of magnets for use in EV motors. Developed and patented by CMI researchers, this process improvement economizes on the use of dysprosium, a heavy rare-earth element, without compromising the properties of the magnets.
4. Recent Policies
Recent pieces of legislation such as the Clean Energy Innovation and Deployment Act of 2020 (the Energy Act), the 2021 Bipartisan Infrastructure Law (formally known as the Infrastructure Investment and Jobs Act), and the 2022 Inflation Reduction Act (IRA) help companies accelerate efforts on supply chain diversification. The Energy Act focuses primarily on fostering innovation through R&D, while the IRA and Bipartisan Infrastructure Law provide funding for infrastructure building and domestic manufacturing to scale innovations.
DOE has been coordinating research and development through itsCritical Minerals and Materials Program in an effort to build secure domestic supply chains of minerals and materials needed for the energy transition. The Energy Act authorized the DOE Critical Minerals and Materials Program to expand its scope, leading to the creation of the Critical Materials Collaborative (CMC) in 2023. CMC is co-chaired by the Office of Fossil Energy and Carbon Management and Office of Energy Efficiency and Renewable Energy (EERE), and it coordinates RD&D across various DOE offices and agencies, Other partners include Advanced Research Projects Agency – Energy (ARPA-E), EERE’s Geothermal Technologies Office (GTO), Hydrogen and Fuel Cell Technologies Office (HFTO), Solar Energy Technologies Office (SETO), Vehicle Technologies Office (VTO), and Wind Energy Technologies Office (WETO), as well as the Office of Electricity (OE), Office of International Affairs (IA), Office of Manufacturing and Energy Supply Chains (MESC), Office of Nuclear Energy (NE), Office of Science (OS), Office of Technology Transitions (OTT), Office of Policy (OP), and Loan Programs Office (LPO). See https://www.energy.gov/eere/articles/doe-launches-critical-materials-collaborative-harness-and-unify-critical-materials. with a potential expansion to include offices from other departments and awardees funded by CMC. The intent of CMC is to enable industry adoption of emerging technologies by acting as a coordinating body among different DOE offices, which focus on different aspects of innovation from basic research to large-scale deployment. Recent CMC efforts emphasize accelerating innovation in all three areas identified in Section 3: diversifying primary production, improving secondary sources, and substitution possibilities.
5. Challenges in Operationalizing the “Midstream” for Critical Mineral Supplies
The midstream part of the EV critical mineral supply chain involves transforming mined raw materials into refined materials suitable for use in EV battery components and magnets, as well as the fabrication of the components themselves. Global processing capacity for several battery minerals has been highly concentrated geographically in China—around 60 percent for cobalt and manganese and over 70 percent for lithium. See figures in Beia Spiller, Sangita Kannan, Michael Toman, “Policy Challenges for Accessing Critical Minerals to Electrify Vehicle Transport,” RFF Report 23-19, December 7, 2023. For magnet rare earths, the concentration in China is even higher. Primary resource availability for battery minerals is much less concentrated geographically than is processing; however, refining of rare earths, including magnet manufacture for EVs, occurs predominantly in China.
High dependence on China for processed EV battery minerals has spurred great interest in the United States in building up a domestic EV battery supply chain. CMI has been an innovation driver and facilitator for shared ideas in DOE’s Critical Materials Strategy for materials critical to clean energy technologies, including materials in EVs, since its inception in 2013. As of the end of 2023, CMI had achieved 202 invention disclosures, 12 R&D 100 Awards, 50 US patents, and 20 licensed technologies. Most achievements so far have been relatively upstream in the R&D cycle, given that CMI’s scope is largely limited to lower technology readiness levels (TRLs).
According to DOE’s inventory of critical materials projects, about two-thirds of DOE-funded projects are at the level of basic research (defined by DOE as TRL 1) or applied research (TRL 2–4). The other one-third involve pilot and demonstration activities (TRL 5–7) and commercialization or deployment (TRL 8–9).
Commercial-scale success is key to strengthening US supply chains. Accordingly, RD&D for critical minerals in the United States needs to increase support for improved midstream technologies and find new mechanisms to spur commercial investment in them. Taking innovation that succeeds at the laboratory level to large-scale deployment requires time for testing and commercial-scale piloting.
Some of the innovation efforts we have mentioned in this paper focus on expanding US capacity to provide primary supplies of critical minerals in the nearer term or to exploit unconventional sources in the longer term as conventional sources become scarcer. Mineral reserves are more widely distributed geographically, however, so the more immediate question concerns midstream mineral processing. The latter is valuable for addressing longer-term supply availability, but in the nearer term, concerns about mineral security may be better addressed by strengthening technological capabilities for mineral processing and supporting innovation in mineral substitution.
Even with increased support for commercial-scale innovation, developing the midstream part of EV mineral supply chains in the United States faces several challenges that will take time to overcome. The expertise and production capacity in this sector exist primarily outside of the United States, having been developed in East Asia for the consumer electronics industry. Consequently, setting up the midstream supply chain elements in the United States entails creating a new industry. Chinese industrial policy has allocated investment capital to building up its critical minerals industry capacity. Overcoming this head start will not be easy or cheap. The United States also is short on several elements related to setting up and operating the supply chains, including equipment needed for product testing and quality assurance (and, at the battery assembly stage, the capacity to manufacture assembly line equipment for making battery cells), as well as the human capital necessary for innovation in the midstream because of a dearth of people with relevant knowledge and experience.
6. Concluding Remarks: The Interface of Innovation with Vehicle Manufacturers
The auto industry is very good at operating complex supply chains over long distances with mixtures of subsidiaries and third parties. However, a lack of in-house expertise and prior operating experience creates challenges for the industry in creating the necessary upstream linkages with EV battery supply chains. Third parties are not known entities with significant track records. That can induce companies to vertically integrate (i.e., create their own subsidiaries), but that also is difficult in this case, given technological and quality assurance uncertainties as well as the unpredictable impacts of innovation. These challenges are exacerbated by the provisions in the IRA that favor domestic battery sourcing despite limited prior experience.
Automakers face further challenges in responding to innovations in battery technologies. They must decide which innovations to scale up in their own product lines and how to do so. The capacity to carry out adequate quality assurance in terms of durability, scale, and performance requires time, testing, and investment. Moreover, the integration of the battery into an EV assembly is a kind of technological “lock-in,” as expensive reengineering of the vehicle is needed to change to a different battery design and configuration. It remains to be seen how the joint evolution of battery technologies and EV designs might affect the flexibility of automakers’ demand for improved batteries over time.
Authors
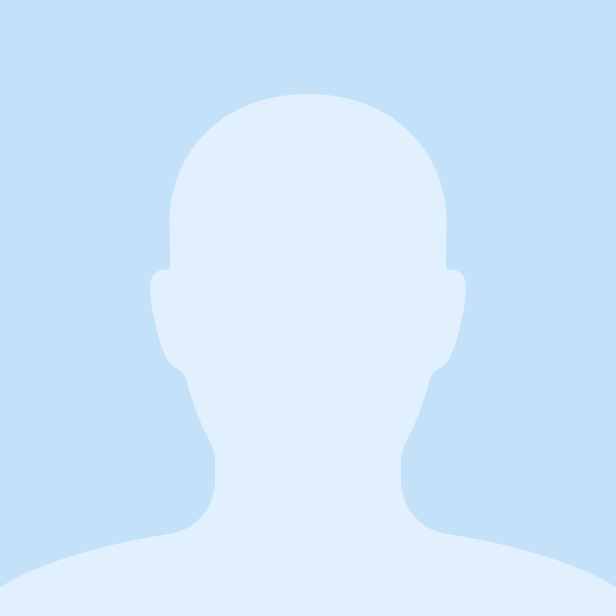
Sangita Gayatri Kannan
PhD Candidate, Colorado School of Mines
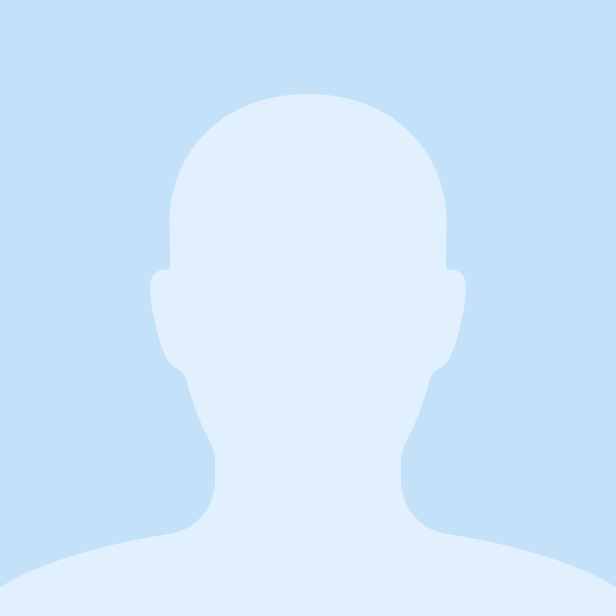
Tinzar Htun
PhD Candidate, Colorado School of Mines